Most mechanical systems require seals. These devices connect mechanisms by avoiding leakage and are critical to machinery performance. A is a compressive seal between two or more surfaces. O-ring seals (sometimes called packing joints) are donut-shaped gaskets that may be employed in both static and dynamic applications.
O-rings are easily made, affordable, and trustworthy, making them one of the most often used seals in equipment across the world.
Here is the Brief History of the O-ring Seals
Niels Christensen, a 72-year-old machinist, submitted the first United States patent for the O-Ring. Born in Tørring, Denmark in 1865, Christensen emigrated to the United States in 1891 and started constructing air braking systems for streetcars.
Niels investigated rubber in the shape of rings in order to develop a sealing solution. He discovered that rubber rings positioned in a groove one and a half times the ring’s minor radius provided a perfect seal for applications such as pistons and cylinders. He was granted a patent in 1939 after two years of application work.
During World War II, the US government recognized Christensen’s O-Ring Seal patent as a “critical war-related item” and granted other corporations the right to produce it. Christensen got a $75,000 payout at the time, and in 1971, more action resulted in $100,000 being given to Christensen’s heirs.
Varieties and Materials of O-Ring Seals
Although O-rings are commonly round, alternative forms, such as squares and X-shapes, are employed for a variety of purposes. Extrusion, compression molding, injection molding, transfer molding, and machining are some of the manufacturing processes used to make O-rings.
Depending on the use, they can be composed of a variety of materials including nitrile rubber, silicone, polyurethane, neoprene, fluorocarbon, and other elastomers. O-ring seal design takes into account quality, quantity, cost, application temperature, sealing pressure, chemical compatibility, movement, action, lubrication, and other factors.
Common O-Ring Seal Applications
Transportation
Severe circumstances necessitate the use of high performance items in industries such as passenger automobiles, heavy duty transportation, and aircraft. Chemical exposure, severe temperatures, and vibration all influence elastomer choices for O-rings. Custom compounds have been developed to fulfill stringent OEM and Tier 1 criteria, and they are constantly modified to meet biofuel and emissions standards.
Medical
In the medical profession, syringes, pumps, filters, and connections require specialized FDA grade O-ring seals.
Oil, Gas, and Industrial
Valves, gas pumps, fittings, dispensers, and storage tanks all require sealing systems that can endure severe temperatures, toxic chemicals, and tremendous compression. Specialty chemicals such as peroxide and triazine-cured perfluoroelastomers provide heat and chemical resistance.
Electronics
O-Rings must be made in clean conditions to meet semiconductor processing and dust protection requirements in consumer electronics. Particulate and contaminant-free O-Ring Seals are available in a variety of compositions.
Food & Beverage:
Specialty 3A sanitary, NSF-61 and water service. O-rings and seals are perfect for food processing, beverage dispensing, and water filtering applications.
Contact Horaiki to learn more about our customized O-Ring Seal solutions, or visit our website to explore our product range.
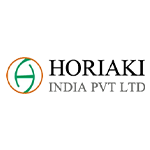
Horiaki India Private Limited
Horiaki India Private Limited was established in the year 1998 with an aim to manufacture and supply premium rubber bonded products in India as well as the international market.